在醫(yī)藥、食品及精密包裝領域,鋁塑泡罩包裝因其高阻隔性、便攜性和可視性被廣泛應用。然而傳統(tǒng)人工或半自動投料方式存在效率低、精度差、浪費嚴重等問題。本文以自動稱重系統(tǒng)為核心,探討其在鋁塑泡罩生產(chǎn)線中實現(xiàn)精準投料的技術路徑、優(yōu)勢及實踐案例,并提出智能化升級方向,為行業(yè)提升生產(chǎn)效能與質量控制提供參考。
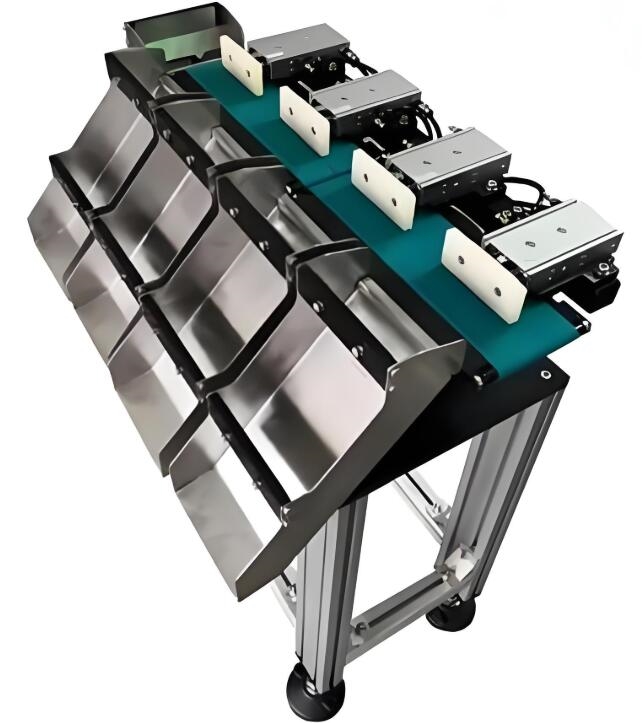
一、鋁塑泡罩包裝工藝與投料挑戰(zhàn)
鋁塑泡罩包裝的工藝流程通常包括:鋁塑復合膜放卷→加熱成型→物料投放→熱封→裁切→輸出成品。其中,精準投料是核心環(huán)節(jié),直接關系到產(chǎn)品劑量準確性、穩(wěn)定性及生產(chǎn)成本。傳統(tǒng)工藝的痛點包括:
1、人工投料誤差大:依賴人工目測或經(jīng)驗判斷,易出現(xiàn)物料過量或不足,導致產(chǎn)品不合格率上升。
2、效率瓶頸:人工操作速度受限,難以匹配高速自動化生產(chǎn)線需求(如每分鐘60~120泡罩)。
3、物料浪費:過量投料造成原料損耗,尤其在高價值藥品或保健品生產(chǎn)中,成本壓力顯著。
4、數(shù)據(jù)追溯困難:人工記錄投料量缺乏實時性與準確性,難以滿足GMP(藥品生產(chǎn)質量管理規(guī)范)要求。
在此背景下,自動稱重系統(tǒng)的引入成為解決上述問題的關鍵技術。
二、自動稱重技術原理與組成
1、系統(tǒng)核心功能
自動稱重系統(tǒng)通過實時監(jiān)測投料重量、動態(tài)調整投料量,并與泡罩成型工藝同步聯(lián)動,實現(xiàn)“精準投放”目標。其核心技術包括:
- 高精度稱重模塊:采用應變片式傳感器或電磁力傳感器,分辨率可達0.01g,適應微量投料需求。
- 動態(tài)補償算法:通過PLC或工控機實時計算投料誤差,結合物料特性(如流動性、密度)進行動態(tài)補償。
- 閉環(huán)控制系統(tǒng):與伺服電機、氣動閥門聯(lián)動,實現(xiàn)“稱量-投放-反饋”的快速循環(huán),響應時間≤100ms。
2、系統(tǒng)組成架構
- 稱重單元:包括稱重斗、傳感器、振動馬達(防止物料滯留)、清潔吹掃裝置。
- 控制單元:PLC主控系統(tǒng)+HMI人機界面,支持參數(shù)設定、數(shù)據(jù)存儲與異常報警。
- 執(zhí)行機構:伺服驅動的投料閥門或螺桿計量裝置,確保物料均勻下落。
- 視覺檢測模塊(可選):通過高速相機拍攝投料過程,輔助判斷物料分布狀態(tài)。
3、與泡罩機協(xié)同機制
系統(tǒng)需與鋁塑泡罩成型設備深度集成:
- 信號同步:接收泡罩成型機的“模具到位”信號后啟動投料,避免物料散落。
- 速度匹配:根據(jù)生產(chǎn)線速度(如每分鐘80次)動態(tài)調整投料節(jié)奏,確保每個泡罩獨立計量。
- 溫度補償:結合熱封溫度數(shù)據(jù),修正物料因環(huán)境溫差導致的體積變化。
三、自動稱重系統(tǒng)的應用優(yōu)勢
1、精準性提升:
- 投料誤差可控制在±0.5%以內(如1g物料誤差≤0.005g),遠超人工操作精度。
2、效率倍增:
- 單次投料周期縮短至0.3~0.5秒,匹配高速泡罩線生產(chǎn)節(jié)拍。
- 人工成本降低70%以上,尤其適用于大批量、連續(xù)性生產(chǎn)場景。
3、質量穩(wěn)定性:
- 消除人為因素干擾,避免因疲勞或操作差異導致的劑量波動。
- 數(shù)據(jù)實時上傳至MES系統(tǒng),支持批次追溯與工藝優(yōu)化。
4、合規(guī)性保障:
- 符合FDA、GMP等法規(guī)對數(shù)據(jù)完整性的要求,投料記錄自動存檔,支持審計追蹤。
- 模塊化設計便于清潔驗證,避免交叉污染風險。
自動稱重系統(tǒng)在鋁塑泡罩線中的應用,標志著包裝生產(chǎn)從“經(jīng)驗依賴”向“數(shù)據(jù)驅動”的轉型。通過技術創(chuàng)新與工藝優(yōu)化,企業(yè)可顯著提升產(chǎn)品質量、降低運營成本,并為智能化工廠建設奠定基礎。